The Comparison of the Mechanical Characteristics of ABS Using Three Different Plastic Production Techniques ()

1. Introduction
Polymers have existed in nature since the beginning of time, and polymers such as DNA, RNA, proteins, and polysaccharides play critical roles in plant and animal life. Man has used naturally occurring polymers as materials for clothing, decoration, shelter, tools, weapons, writing materials, and other purposes since the dawn of time [1] .
A polymer is a substance made up of molecules with long sequences of one or more atom species or groups of atoms connected by primary, usually covalent, bonds. The emphasis on substance in this definition is intended to emphasize that, while the terms polymer and macromolecule are used interchangeably [1] .
Polymer composites are becoming more popular in the plastics industry due to their high strength and low density. Short fiber reinforced thermoplastic polymer composites are widely used in a wide range of applications, including aircraft, aerospace, and the automotive industry [2] . Their structure determines their properties, which are heavily influenced by processing conditions and composition. When samples are printed in an injection mold, a stuck material will form at the tip of the injection nozzle. This is caused by the material's incorrect melting point. Warping of the specimen occurs when samples are manufactured using an additive manufacturing procedure, which can be overcome by putting gum on the printer bed. When the material becomes trapped in the nozzle, the problem can be remedied by increasing the hot end temperature over the melting point of the material. When samples are printed in a compression mold, the ABS material granules are improperly melted. This is because the mold plates were not heated to the desired temperature.
1.1. Acrylonitrile Butadiene Styrene (ABS) Polymer
ABS is a terpolymer formed by polymerizing styrene and acrylonitrile with polybutadiene. The proportions of acrylonitrile can range from 15% to 35%, butadiene from 5% to 30%, and styrene from 40% to 60%. As a result, a long polybutadiene chain is crisscrossed with shorter polybutadiene chains (styrene-co-acrylonitrile). Because polar nitrile groups from neighboring chains attract and bind the chains together, ABS is stronger than pure polystyrene. Acrylonitrile also adds chemical resistance, fatigue resistance, hardness, and rigidity while raising the heat deflection temperature. The styrene imparts a shiny, impervious surface to the plastic, as well as hardness, rigidity, and improved processing ease [3] .
Acrylonitrile-butadiene-styrene (ABS) polymers are a versatile family of easily processable resins used to create products with excellent toughness, dimensional stability, and chemical resistance. Transparency, unique coloration effects, higher heat performance, and flame retardancy are all available as special product features. ABS is a thermoplastic matrix of styrene, acrylonitrile copolymer (SAN), and particulate rubber, typically polybutadiene or a butadiene copolymer. The presence of SAN chemically attached or “grafted” to elastomeric particles allows the rubber to be compatible with the SAN component. Changing structural and compositional parameters allows for significant flexibility in tailoring properties to meet specific product requirements [4] .
ABS and substrates are becoming more popular because they can be produced using modern additive manufacturing (AM) processes and can be plated. Examples of AM technology are stereolithography, selective laser sintering, fused deposition modeling, laminated object manufacturing, solid ground curing, and solid creation system [5] . (Figure 1 and Figure 2)
ABS plastic can be traced back to the mid-1940s. Since the 1940s, acrylonitrile-styrene copolymers have been used, and the disadvantages of these copolymers have led to the incorporation of a third monomer, butadiene rubber. Butadiene gave the plastic greater strength and impact resistance. During the final years of World War II, high molecular mass butadiene-acrylonitrile copolymers and styrene-acrylonitrile copolymers were used to make bulletproof polymer sheets. Because of their low thermoplastic flow properties, the copolymer systems had high impact strength. The first ABS products were molded parts such as sheets, profiles, and pipes. The invention of injection molding and graft polymerization techniques paved the way for the revolutionization of ABS plastic applications [5] .
1.2. Properties of ABS
When compared to other common polymers, ABS has superior mechanical properties such as impact resistance, toughness, and rigidity [3] . To improve impact resistance, toughness, and heat resistance, a variety of modifications can be made.
ABS plastics are primarily used for mechanical purposes but also have electrical properties that are constant across a wide range of frequencies. Temperature and atmospheric humidity have little effect on these properties within the acceptable operating temperature range [6] . The properties of ABS plastic have shown in the following Table 1.
1.3. Applications of ABS Polymer
ABS has numerous applications in a variety of industries. The following is a list of common applications for each type, as well as some recent examples of more specific applications. Some of the applications include crash helmets, pipes, vacuum cleaner bodies, washing machine housings, air conditioner grilles, chairs, attached cases, toys, and pipes. calculating machine, electric shaver housings, tape recorder housings; electric fan bases, hair drier grips, audio speaker cabinets, telephone sets, pencils, bobbins, and battery cases Radiator grilles, instrument panels, steering shaft covers, air conditioning ducts, and grilles, heater ducts and grilles, electric appliances such as speaker cabinets, portable TV cabinets, TV back covers, hair drier housings, and iron handles, instrument panels, steering shaft covers, air conditioning ducts, heater ducts, and grilles, heater ducts and grilles, heater ducts and grilles, heater ducts and grilles, heater ducts [7] .
2. Specimen and Material
2.1. Specimen Preparation
In this project, ASTM D638 Type IV dog-bone test specimens were used. The dimensions of the specimen are as follows in Figure 3 and Table 2 [8] . Non-rigid or semi-rigid plastics should indeed be tested with ASTM D638 Type IV test specimens. Most researchers have used ASTM D638 Type I or Type IV dog-bone geometry test specimens or similar designs to evaluate the mechanical performance of polymers under static loading [9] .
2.2. Material Selection
ABS granules were used in both Injection and compression molding, whereas this project made use of high-quality ABS (Acrylonitrile butadiene styrene) filament (blue) from Real Filament Company in the Netherlands. The filament is
![]()
Table 1. Mechanical properties of ABS [7] .
not prohibitively expensive, costing 25?for 1 kg. Filaments are typically available in two diameters, 1.75 mm and 2.85 mm, with 1.75 mm being the most common in FDM type 3D-Printers. (Figure 4 and Figure 5)
![]()
Figure 3. ASTM D638 type IV Test specimen.
![]()
Table 2. ASTM D638 Type IV dimensions [8] .
3. Manufacturing Processes of ABS Plastic
3.1. Injection Molding
The injection molding process is one of the most common methods for producing large quantities of plastic parts. It is a repetitive process in which melted polymer or plastic is injected into a cavity or cavities, depending on the requirement, packed under pressure, and cooled until the part solidifies [10] . Injection molding is now regarded as one of the most important processes used in the manufacture of plastic products. Injection molding accounts for more than one-third of all thermoplastic materials and more than half of all polymer processing equipment.
The main advantage of injection molding is its ability to mass-produce products. The basic principle of injection molding is very straightforward. The plastic material in pellet form is gradually heated until it becomes a viscous melt. The product is then pushed or rammed into a closed mold or cavity that defines its shape [11] .
For many years, product design or innovation was the primary driver of plastic industry innovation or development. The items were supposed to serve a variety of functions, reducing the number of molded components while also benefiting the companies [10] [11] . This has not been the case in recent years, and innovation in process control or process functioning is now recognized as a critical component of the plastics industry's future growth.
Because the melting point of ABS is between 180˚C and 200˚C, the injection molding melt temperature in this project is 220˚C. The mold temperature is stated to be 80˚C - 90˚C. The injection pressure is 90 MPa, and the mass volume is 27 cm3. (Figure 6)
The samples are made by ASTM D638 Type IV standards. (Figure 7)
3.2. Compression Molding
Compressive testing demonstrates how a material will react when compressed.
Compression testing can identify a material’s behavior or response under crushing loads and evaluate its plastic flow behavior and ductile fracture limits [12] . Compression molding, also known as matched die molding, is one of the oldest materials processing techniques [13] . The basic procedure entails heating a thermoset resin under high pressure within a closed mold cavity until the resin cures via a chemical reaction of cross-linking polymeric chains. Under pressure, the resin liquefies and flows, conforming to the shape of the mold cavity before hardening to form the desired part or product. When the part is sufficiently cooled and strong, it is removed from the mold, and the cycle is complete, though the curing reaction continues while cooling to room temperature [13] . The viscosity of thermoplastic polymers varies significantly with changes in temperature, density, and shear rate. The relative density of the ABS filaments is 1.210 g/cm3, which is quite high [14] .
Compression molding procedure:
1) Turn on the machine by pressing the power button.
2) Configure the desired process parameters, such as plate heating temperatures, melding force, mold closure speeds, and cycle times.
3) Without the polymer, close the mold.
4) Open the press safety door and place the mold in the center of the lower plate, then close the safety door.
5) At the temperature set point, turn on the upper and lower plate heaters.
6) Close the press, contacting the mold's lower and upper surfaces with the corresponding plates, and hold until the mold reaches the molding temperature.
7) Remove the heated mold from the press.
8) Split the mold in half and open it.
9) Wax the inside cavity surfaces of both mold halves with mold-release wax.
10) Pour a measured amount of resin (charge) into the lower half cavity, tilting it side to side to evenly distribute the charge.
11) Align the upper and lower mold halves and reposition the closed mold on the press lower plate.
12) Close the safety door and stroke the press to pressurize the mold cavity to an intermediate level for a predetermined amount of time, then release the clamping force to degas the cavity.
13) Apply maximum pressure and hold for the required compression time to complete the curing.
14) Remove the mold from the press and turn off the plate heaters.
15) Allow the mold to cool before opening it and removing the part.
16) Use the plate cooling circuit to move water through internal cooling channels to lower and upper plate temperatures. (Figures 8-10)
3.3. Additive Manufacturing
3D printing is also termed Additive Manufacturing. In the earlier 1980s, additive manufacturing was mostly used for the manufacturing of prototypes, but, in these years, their usage has increased due to their precision, repeatability, and production costs. Depending upon their usage, there are many types of 3D printing. Some major types are SLA (Stereolithography), FDM/FFF (Fused Deposition Modelling/Fused Filament Fabrication), Material Extrusion, Binder Jetting, Powder Jetting, Direct Energy Deposition, etc. Among all types of 3D Printing, FDM is the most effective technique to print prototypes as well as custom thermoplastic components [15] . Additive manufacturing is the process of
creating an object one layer at a time. It is the inverse of subtractive manufacturing, which involves removing material from a solid block until the finished product is complete. Technically, additive manufacturing can refer to any process that creates a product by building it from the ground up, including 3D printing [16] .
For building parts layer by layer using CAD models that allow for the rapid and low-cost production of parts of varying complexity. Because it does not require tooling and reduces material waste, AM provides dependable, flexible, and cost-effective manufacturing methods [17] . 3D printing has grown in popularity in a variety of industries, including aerospace, defense, automotive, biomedical, and dental [18] [19] . Improved mechanical properties, high dimensional accuracy, and manufacturing speed are driving widespread industrial adoption of FDM technology. Extruding polymer and polymer composite materials through a hot nozzle to form a raster with varying shapes, thicknesses, widths, and heights is what FDM is all about.
3.4. Fused Deposition Modelling
The FDM process allows the manufacturing of the parts or prototypes by extruding material like ABS, PLA, Onyx, Nylon, etc. through a nozzle that traverses in X and Y to create each two-dimensional layer. Instructions for the nozzle directions are given by STL file, which consists of G-Code [20] . Fused deposition modeling (FDM) is an additive manufacturing process in which a thin plastic filament feeds a machine where a print head melts and extrudes it to a thickness of 0.25 mm [21] . Among all other additive manufacturing techniques, fused deposition modeling (FDM) plays a dominant role in all kinds of industries from small-scale to large-scale due to its low cost and its ease of operation, even by non-professionals. FDM is a process in which a circular cross-sectional filament of a predefined diameter is made to push into the hot end using a feeder with a defined speed, and melted material is exited from the nozzle attached to the hot end, which follows a defined path to construct a specimen layer-by-layer [22] .
The widespread usage of this system has been recently boosted by the expiration of the FDM patent and the subsequent worldwide development of low-cost machines by a huge number of companies [23] . The main advantages of this process are that no chemical post-processing is required, there are no resins to cure, and the machine and materials are less expensive, resulting in a more cost-effective process [21] . In this study, a Creality 2020 Ender-3, V2 model FDM 3D-Printer was used. (Figure 11 and Figure 12) For the movement of the extruder head and print bed, the mechanical axes are arranged in the Cartesian
XZ-Head order, i.e., the extruder head moves in the X and Z axes while the print bed moves in the Y direction. The maximum possible dimensions of the machine are 220 * 220 * 250 mm (L*BH*) [21] . The maximum bed temperature, extruder temperature, and printing speed are all set at 100˚C, 250˚C, and 180 mm/sec, respectively [24] .
The test specimen was printed under ambient pressure conditions on a Creality Ender-3 V2 FDM 3D printer with a single extruder with a nozzle diameter of 0.7 mm. (Figure 13) The following parameters were used to print the test specimen, as shown in Table 3.
4. Mechanical Tests: Tensile Test ASTM D638
The basic idea behind a tensile test is to clamp a material sample between two fixtures known as “grips”. The material’s length and cross-sectional area are known. The material is then held at one end while the other is locked, and
![]()
Table 3. 3D printer parameters for the test specimen [21] .
weight is applied [25] .
A piece of material is held at both ends by an apparatus, which gradually pulls it lengthwise until it fractures. The pulling force is referred to as a load, and it is plotted against the material’s length change, or displacement [7] . The displacement is converted to a strain value and the load to a stress value.
This test yielded a graph of load (weight) versus displacement (the amount it stretched). Comparing different materials may be difficult because the amount of weight required to stretch material is dependent on its size (and, of course, its qualities). The ability to make thorough comparisons is critical when designing for structural applications where the material must withstand forces [26] . (Figure 14)
5. Results and Discussions: Tensile Test ASTM D 638 Analysis
5.1. Comparison of Young’s Modulus of ABS in Different Test Speeds
According to Graph 1, the ABS polymer’s Young’s modulus is 3829 MPa, 2885 MPa, and 2057 MPa for Injection molding, Compression molding, and 3D printing, respectively. This leads us to the conclusion that when compared to compression-molded samples and 3D-printed samples, injection-molded samples have a higher Young’s modulus at 5 mm/min test speed.
According to Graph 2, the ABS polymer’s Young’s modulus is 3655 MPa, 2801 MPa, and 2016 MPa for Injection molding, Compression molding, and 3D printing, respectively. This leads us to the conclusion that when compared to compression-molded samples and 3D-printed samples, injection-molded samples have a higher Young’s modulus at 15 mm/min test speed.
According to Graph 3, the ABS polymer’s Young’s modulus is 3602 MPa, 2849 MPa, and 1979 MPa for Injection molding, Compression molding, and 3D
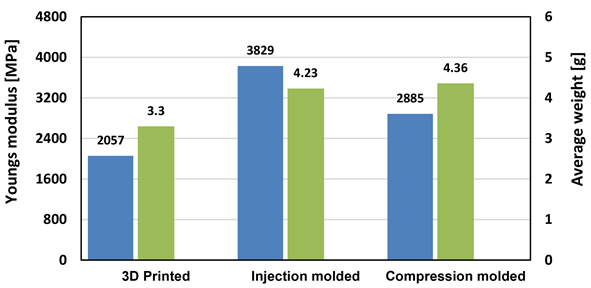
Graph 1. Comparison of Young’s modulus of ABS in 5 mm/min.
![]()
Graph 2. Comparison of Young’s modulus of ABS in 15 mm/min.
![]()
Graph 3. Comparison of Young’s modulus of ABS in 25 mm/min.
printing, respectively. This leads us to the conclusion that when compared to compression-molded samples and 3D-printed samples, injection-molded samples have a higher Young’s modulus at 25mm/min test speed.
In each of the abovementioned instances, Young’s modulus of the ABS polymer gradually fell as the test speed increased in increments of 10 mm/min starting at 5 mm/min and ending at 25 mm/min.
5.2. Comparison of Yield Strength and Yield Strain of ABS in Different Test Speeds
The injection-molded sample’s yield strength and yield strain are shown in Graph 4 and are, respectively, 68.56 MPa and 3.13%. The 3D-printed molded sample’s yield strength and strain are 42.45 MPa and 2.81%, respectively. The compression molded sample’s yield strength and yield strains are 40.83 MPa and 2.43%, respectively. Therefore, at a test speed of 5 mm/min, the yield strength and yield strain of the injection-molded sample are higher than those of the 3D-printed sample and the compression-molded sample.
The injection-molded sample’s yield strength and yield strain are shown in Graph 5 and are, respectively, 69.2 MPa and 3.2%. The 3D-printed molded sample’s yield strength and strain are 43.65 MPa and 2.93%, respectively. The compression molded sample’s yield strength and yield strains are 39.19 MPa and 2.3%, respectively. Therefore, at a test speed of 15 mm/min, the injection-molded sample yield strength and yield strain are higher than those of the 3D-printed and compression-molded samples.
The injection-molded sample’s yield strength and yield strain are shown in Graph 6 and are, respectively, 7.46 MPa and 3.21%. The 3D-printed molded
![]()
Graph 4. Comparison of yield strength & yield strain of ABS in 5 mm/min.
![]()
Graph 5. Comparison of yield strength & yield strain of ABS in 15 mm/min.
sample’s yield strength and strain are 44.36 MPa and 3.01%, respectively. The compression molded sample’s yield strength and yield strains are 42.45 MPa and 2.55%, respectively. Therefore, at a test speed of 25 mm/min, the injection-molded sample yield strength and yield strain are higher than those of the 3D-printed and compression-molded samples.
When evaluated at test speeds of 5 mm/min, 15 mm/min, and 25 mm/min in all the above-mentioned Graph 4, Graph 5, and Graph 6, both yield strength and yield strain gradually increase in three different plastic processes.
5.3. Comparison of Esec Modulus of ABS in Different Test Speeds
Esec modulus values for ABS polymer samples manufactured using injection molding, compression molding, and 3D printing are 2696 MPa, 2106 MPa, and 1564 MPa, respectively, in the abovementioned Graph 7. As a result, when examined at a speed of 5 mm/min, ABS polymer specimens from injection-molded samples are superior to those from compression-molded samples and 3D-printed samples.
Esec modulus values for ABS polymer samples manufactured using injection molding, compression molding, and 3D printing are 2644 MPa, 2076 MPa, and 1538 MPa, respectively, in the abovementioned Graph 8. As a result, when examined at a speed of 15 mm/min, ABS polymer specimens from injection-molded samples are superior to those from compression-molded samples and 3D-printed samples.
![]()
Graph 6. Comparison of yield strength & yield strain of ABS in 25 mm/min.
![]()
Graph 7. Comparison of Esec modulus of ABS in 5 mm/min.
![]()
Graph 8. Comparison of Esec modulus of ABS in 15 mm/min.
![]()
Graph 9. Comparison of Esec modulus of ABS in 25 mm/min.
Esec modulus values for ABS polymer samples manufactured using injection molding, compression molding, and 3D printing are 2651 MPa, 2021 MPa, and 1531 MPa, respectively, in the abovementioned Graph 9. As a result, when examined at a speed of 5mm/min, ABS polymer specimens from injection-molded samples are superior to those from compression-molded samples and 3D-printed samples.
In the three plastic processing methods shown in the abovementioned Graphs 7-9, the Esec modulus of ABS polymer steadily drops as the test speed increases from 5 mm/min to 25 mm/min with a 10 mm/min interval. Therefore, the ABS polymer’s Esec modulus of Injection molded samples is larger than those of the compression-molded samples and the 3D-printed samples.
6. Conclusions
The results of the tests and measurements show that the different methods of producing ABS samples influence their mechanical properties. Although the differences in Young’s modulus strength between compression molded and injection molded samples are minor, the biggest difference is in 3D printed samples. This can be caused by different macromolecular chain arrangements in the material structure because of different deformation inside the mold. During injection molding, the material fills the volume of the cavity in one direction, exposing it to greater shear deformation, primarily in the direction of flow. In the case of compression molding, however, the material is subjected to much lower shearing deformation and a short multi-directional flow. But in the case of 3D printing technology is an additive printing process that creates objects by building up layers of material, while plastic injection molding uses a mold that is filled with molten material that cools and hardens to produce parts and components and in compression molded same, but the pressure is applied a lot more than 3D printing. The following research will validate the previously examined mechanical properties of other commonly used shapes of testing samples, as well as extend the research to cover other useful types of ABS compounds.
But in the future, we can try to produce samples of 3D printing with stronger or minimal strength difference compared to injection molding by printing samples with more pressure and temperature in closed champers like autoclave, etc.
However, when we compared the yield strength of all the samples produced in the above three processes, 3D-printed samples outperformed compression molding samples. This is because the pressure applied in compression molding samples is greater than deformation via heat, causing the material’s strength to be lower.