Dynamic Failure Model of Thin Coal and Rock Mass under Uniform Impact Load ()
1. Introduction
With the increasing demand for mineral resources and the continuous consumption of shallow resources, the mining of domestic and foreign coal mines and metal mines has gradually shifted to the deep [1] [2]. During the excavation of deep coal and rock mass, the radical stress of the free face changes from three-dimensional compression state to two-dimensional stress, so many mines have suffered from dynamic disasters, such as coal and gas outburst, rock burst, rock caving and other dynamic disasters in deep mining, which is often accompanied by plate crack, spalling and other disasters, seriously affecting the stability of stope and roadway [3] [4]. Fairhurst et al. [5] first described the plate cracking failure in detail which is approximately parallel to the wall of surrounding rock and called the phenomenon of plate cracking failure as spalling or slabbing [6]. Feng Fan et al. believed that the plate cracking failure could be defined as a serious of macroscopic cracks parallel to the excavation boundary of the deep hard rock chamber. When the thickness of the plate is far less than the span of the plate in length, the experiment is carried out within the framework of small deflection theory of transverse vibration, with three factors the vertical shear deformation, extrusion deformation and moment of inertia been ignored in the basic equation of three-dimensional elastodynamics. The classic thin plate theory called Poisson Kirchhoff worked out in the experiment has been widely used in many industries, such as mining and construction [7] [8]. Based on the thin plate model, many scholars have carried out extensive researches on the mechanism and mechanical behavior of coal and rock mass plate cracking failure and plate cracking (spalling) buckling rock burst. However, due to the vibration of the thin plate under the action of external force has a significant impact on its mechanical properties, so that researches on the failure mechanism and development trend of coal and rock mass under dynamic load disturbance are still in the qualitative analysis stage, which could not provide strong support for fundamentally revealing the occurrence mechanism of coal and rock dynamic disaster. At present, it is still significant to construct a complete and consistent understanding of coal and rock dynamic disasters no matter in academic or in coal and mines industries [9] [10] [11] [12].
Therefore, this research mainly focused on the dynamic response characteristic and failure mechanism of thin coal and rock mass based on rectangular thin plate model. The Hamilton dual system was used to study the dynamic response characteristics of thin coal and rock mass under forced vibration. Besides, based on the characteristics of uniform impact load, the effective vibration mode solution of thin coal and rock mass under forced vibration was studied by using Duhamel integral principle, and the dynamic damage failure process and mechanism of thin coal and rock mass were analyzed, which are beneficial to revealing the mechanism of coal rock dynamic disaster.
2. Calculation Model of Dynamic Response of Thin Coal and Rock Mass
2.1. Vibration Control Equation of Thin Coal and Rock Mass
The size requirements of the thin rectangular plate (the ratio of the thickness to the width of the plate is between 1/5 and 1/80). The thin plate model can resist bending and torsion and can also bear the stress in the plane. And the neutral plane was used to establish the coordinate system as shown in Figure 1, which was used to study the dynamic response characteristics and failure mechanism of thin coal and rock mass subjected to forced vibration under uniform impact load.
Supposing the density of the thin plate was ρ, the thickness was h, the size was a × b, the elastic modulus was E, and the Poisson’s ratio was υ. Under the impact load
, according to the transient equilibrium conditions of the internal mechanics of the thin plate, the differential equation of the forced vibration of the thin plate can be derived [13]:
(1)
Among them,
was the deflection, D was the bending stiffness.
Firstly, the homogeneous equation of Equation (1) was solved.
When
, the free vibration differential equation of the thin plate was [14]:
(2)
Supposing that the vibration of a thin plate had the following change rule of the harmonic oscillator with time:
(3)
Among them, ω was the natural frequency and
was the deflection mode function of the thin plate. Substituting Equation (3) into Equation (2), then:
(4)
Among them,
.
![]()
Figure 1. Coordinate system of thin rectangular plate.
2.2. Hamilton Dual Vibration Equation of Thin Coal and Rock Mass
In order to decouple the physical quantities in the control equations, it was necessary to introduce the Hamilton dual equations [15] [16].
If
, from the force analysis results of the thin plate, the relationship between the physical quantities were:
(5)
(6)
(7)
Among them, Mx, My, Mxy, Qx, Qy, Vx, Vy were the bending moment, torque, transverse shear force, and transverse total shear force of the thin plate, respectively. If vector
, then the dual equation of Hamilton system was:
(8)
That was,
2.3. Solving the Hamilton Dual Equations
Based on the symplectic geometry method [15], the Equation (8) was solved by the separation variable method. The deflection modes in the x and y directions were W(x) and W(y), respectively, and their specific forms can be written as [17] [18] [19]:
(9)
(10)
Among them:
,
,
,
,
3. Deflection Vibration Equation of Thin Coal and Rock Mass
3.1. Deflection Vibration Equation of the Thin Plate (C-C-C-C)
The density of sheet coal bodies is h, the thickness is h, and the size is a × b, and the elastic modality is E. The four-side solid sheet coal body (C-C-C-C) along the y direction boundary condition is:
,
;
,
.
Substitute (10) available:
If the above formula had a solution, the determinant of the coefficient matrix on the left was zero, and the frequency equation along the y direction was:
(11)
To make C2 = 1, the combined frequency equation solves:
Among them,
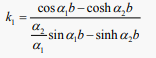
Thus,
Similarly,
Among them,
Therefore, the vibration equation of the free vibration of the Thin Coal and Rock Mass (C-C-C-C) is:
(12)
3.2. The Vibration Function of the Free Vibration of the Thin Coal and Rock Mass (S-C-S-C)
As for a thin plate with two sides fixed and other two sides simply supported (S-C-S-C), the boundary conditions along the x direction (simple supported side) were:
,
;
,
.
Substitute (9) available,
Available from the upper formula,
;

If there is an upper solution, the left coefficient matrix is zero, resulting in a frequency equation along the x direction:
Make, B1 = 1, D1 = 0. So:
Therefore, the vibration function of the free vibration of Thin Coal and Rock Mass (S-C-S-C) is:
(13)
4. The Vibrational Function of the Forced Vibration of a Thin Coal and Rock Mass
4.1. Solving the Control Equation
The form of the solution of the non-homogeneous Equation (1) can be written as:
(14)
Substituting Equation (13) into Equation (1):
Because,
Thus,
Both sides multiply by
at the same time, according to the orthogonality of the deflection vibration mode function, it can be derived [20]:
Integrating over the entire plane area, then:
If,
Then,
According to Duhamel’ integral,
Assuming that the pressure of the explosion impact load on the thin plate could be regarded as an instantaneous uniform load, it had the following form:
So:
Therefore, the solution of the vibration control Equation (1) of the thin plate under uniform impact was:
(15)
4.2. Effective Main Vibration Mode of Thin Coal and Rock Mass
4.2.1. Main Vibration Mode of Thin Coal and Rock Mass (C-C-C-C)
The parameter values of the thin plate were: h = 0.06 m, ρ = 2800 kg/m3, E = 72 × 109 Pa, υ = 0.3, a × b = 3 m × 3.6 m. Combined with the frequency equation of the Thin Coal and Rock Mass (C-C-C-C), the Newton iteration method can be used to solve the main vibration mode. The calculated values of the first 10 order vibration parameters were shown in Table 1, and the value of the first 10 order vibration parameters of the Thin Coal and Rock Mass (C-C-C-C) under the impact load were shown in Table 2. It can be derived from Table 2 that the first-order, fifth order, and sixth-order vibration functions were the main modes, and the natural frequencies of their vibrations were 308 Hz, 975 Hz, 1309 Hz, respectively. The analysis showed that the 5th order coefficient An/q0 was about 9.4% of the 1st order coefficient; the 6th order coefficient An/q0 was about 4.9% of the 1st order coefficient.
![]()
Table 1. The first 10 vibration parameters of the main mode of rectangular thin coal and rock mass (C-C-C-C).
![]()
Table 2. The first 10 order vibration parameters values of coal and rock mass (C-C-C-C) under impact load.
4.2.2. The Main Vibration Mode of the s Thin Coal and Rock Mass (S-C-S-C)
Combined with the frequency equation, can be derived from Table 3 that the first 10-order vibration parameters of the main vibration modal function of the Thin Coal and Rock Mass (S-C-S-C) (S-C-S-C) (short branch on the left and right, solid branch on the upper and lower sides) are solved by Newton iterative method. The first ten-order vibration parameter values of the S-C-S-C thin sheet coal rock bodies on both sides of the fixed branch under the average impact load are set out in Table 4. Available: 1st, 5th, 6th and 10th order vibration functions are valid main vibration types, and their inherent vibration frequencies are 230Hz, 943 Hz, 999 Hz, 1680 Hz. The 5-order coefficient is about 10.6% of the first-order coefficient, the 6-order coefficient is about 2.8% of the first-order coefficient, and the 10-order coefficient is about 1.3% of the first-order coefficient.
4.2.3. Dynamic Destruction Process of the Thin Coal and Rock Mass (C-C-C-C)
Based on the third strength criterion, the dynamic distribution of the maximum shear stress in the thin plate (C-C-C-C) was shown in Figures 2-4. It can be seen
![]()
Table 3. The first 10 order vibration parameters of the main mode of thin rectangular coal and rock mass (S-C-S-C).
![]()
Table 4. The first 10 order vibration parameters values of coal and rock mass (S-C-S-C) under impact load.
from the figures that the maximum shear stress of the first order main mode was mainly distributed in the middle area of the four sides; the maximum shear stress of the fifth order main mode was mainly distributed in the middle area of the two short sides, the center area of the thin plate and the center area along the long axis of the thin plate; the maximum shear stress of the sixth order main mode was mainly distributed in the middle area of two long edges, the center area of the sheet and the center area along the short axis of the sheet.
![]()
Figure 2. The maximum shear of the first order main mode (C-C-C-C).
![]()
Figure 3. The maximum shear of the fifth order main mode (C-C-C-C).
![]()
Figure 4. The maximum shear of the sixth order main mode (C-C-C-C).
Therefore, the dynamic failure process was as follows: under the uniform impact load, the location of the rectangular plate (C-C-C-C) prone to damage was located in the middle of the four sides and the central area of the rectangular plate, mainly along the central area of the long axis of the plate, and then along the central area of the short axis (x axis).
4.2.4. Dynamic Destruction Process of the Thin Coal and Rock Mass (S-C-S-C)
Based on the third strength theory, the dynamic distribution of the maximum shear stress in the thin plate (S-C-S-C) under the impact load was shown in Figures 5-8. It can be seen from the figure that the maximum shear stress of the first order main mode were mainly distributed in the middle region of the short side and four concentration regions of the long side; the maximum shear stress of the fifth order mode were mainly distributed in the middle region of the two short sides and the center region along the long axis of the thin plate The maximum shear stress of the sixth order mode were mainly distributed along the center of the short axis of the thin plate; the maximum shear stress of the tenth order mode were distributed in each area.
![]()
Figure 5. The maximum shear of the first order main mode (S-C-S-C).
![]()
Figure 6. The maximum shear of the fifth order main mode (S-C-S-C).
![]()
Figure 7. The maximum shear of the sixth order main mode (S-C-S-C).
![]()
Figure 8. The maximum shear of the tenth order main mode (S-C-S-C).
The dynamic failure process was as follows: under the impact load, the damage of the Thin Coal and Rock Mass (S-C-S-C) was located in the middle of the short side and the four concentration areas of the long side; it was mainly along the long axis of the thin plate, followed by the central area along the short axis.
5. Simulation of Dynamic Destruction Process of Thin Coal and Rock Mass
Based on Ls-DYNA software, the PLASTIC_KINEMATIC material model was used to simulate and analyze the destruction process of thin plates. The dynamic failure process of the thin Coal and Rock Mass (C-C-C-C) was as follows: first, the crack occurred at the center of the short side of the thin plate, and the damage occurred at the center of the long side of the thin plate, then the central area of the thin plate. The damage direction mainly developed along the long axis, and the second along the short axis or width. In the end, the main damage area were around the thin plate, the central area, and the area along the central long axis, as shown in Figure 9.
The dynamic failure process of the Both sides are firmly supported and both sides simply supported Thin Coal and Rock Mass (S-C-S-C) was as follows: first, cracks occurred in the middle of the short side of the thin plate and the four concentration areas on the long side, and then the damage occurred on the long side of the thin plate. The failure direction of the thin plate mainly developed along the long axis. It would develop toward the center of the sheet al.ong the short axis or width, as shown in Figure 10.
6. Discussion on Dynamic Failure Mechanism of Thin Coal and Rock Mass
Under the impact load, the vibration of thin plate (C-C-C-C) was dominated by the first order (dominant frequency), followed by the fifth order and the sixth order. According to Figure 2, the maximum shear stress in the central area of the four sides of the first order mode was obviously greater than that in the central area, so the location of the first failure should be the central area of the four sides, followed by the central area of the thin plate. According to Figure 3, in addition to the maximum shear stress concentration in the central area of the four sides, the fifth order mode also had the maximum shear concentration along the long axis of the thin plate, as a result, the location of the failure should be from the center along the long axis to the outside; at the same time, it can be seen from Figure 4 that the sixth order mode also had the maximum shear concentration along the short axis, so the location of the failure would also have a relatively small range of outward expansion along the short axis. The whole development process was consistent with the failure process simulated in Figure 9.
Similarly, the analysis of the vibration of the thin plate (S-C-S-C) was dominated by the first order (main frequency), followed by the fifth order, the sixth order, and the tenth order. From Figures 5-8, it can be seen that the maximum shear of the first order main mode were mainly distributed in the middle of the short side and the four concentration areas of the long side, which were also the locations where the thin plate first break; the maximum shear of the fifth order mode were mainly distributed in the center of the two short sides and along the long axis of the thin plate, which was the main direction of crack development;
![]()
Figure 9. Dynamic failure process of thin rectangular coal and rock mass (C-C-C-C).
![]()
Figure 10. Dynamic failure process of thin rectangular coal and rock massr (S-C-S-C).
the maximum shear of the 6th order mode were mainly distributed along the short axis, which was also the main direction of crack development. Eventually, the crack would develop towards the central area of the thin plate; the maximum shear of the 10th order mode was distributed in each area of the thin plate, but its amplitude was relatively small even can be ignored. The entire destruction development process was consistent with the destruction process simulated in Figure 10.
Based on the above analysis, it can be concluded that the initial failure position of the thin plate (C-C-C-C) and the thin plate (S-C-S-C) can be inferred from the dynamic distribution characteristics of the first order mode (main frequency), and the development direction and trend of the failure can be judged from the fifth and sixth order main modes. The three main modes constitute the effective main vibration mode under the impact load of the rectangular Thin Coal and Rock Mass mode.
7. Conclusions
1) Based on the rectangular thin plate model, the dual equation of Hamilton system for free vibration of thin coal and rock mass was established; based on the orthogonality of mode function and Duhame integral, the dynamic deflection distribution equation of thin coal and rock mass under uniform impact load was derived.
2) Based on the third strength theory and numerical simulation results, the dynamic damage process of thin coal and rock mass under impact load was analyzed, the initial failure position of the rectangular thin plate can be inferred from the dynamic distribution characteristics of the first order mode (main frequency), and the development direction and trend of the failure can be judged from the fifth and sixth order main modes.
3) The first order main mode, fifth and sixth order main modes constitute the thin Coal and Rock Mass (C-C-C-C) and (S-C-S-C) effective main vibration mode equation synthetically under uniform impact load.
Fund Projects
State Key Research and Development Program Funding (2016 YFC0801800), National Natural Science Foundation Of China Project (51804311), China Mining University (Beijing) Deep Rock and Soil Forces and Underground Engineering National Key Laboratory Open Fund Project (SKLGDUEK1818).