Performance Survey of PVC Insulation of LC/Gecamines Electrical Cables Subjected to Ageing and Its Life Span Evaluation ()
1. Introduction
The factory of rolling and cable mills L.C acronym, was created in the middle of the Second World War during the occupation of Belgium by the German Nazis. The purpose was to mitigate the importation and production difficulties of the manufactured products in steels (cables, flats, tubes) by Belgium. Since 1975, the factory has been annexed to the Congolese mining giant GECAMINES under the name of “Rolling mills and cable factories main office” [1]. Previously, about 95% of companies in RDC used the insulated electrical cables from L.C/Gecamines for their internal installations. The cables are insulating with various types of polymers [2]. The insulation can age; it can suffer from defects due to operating conditions, and at the same time cause invaluable damage at the industry [3]. Therefore, the accurate prediction of the service life and operating conditions of electrical cables is obviously becoming an economic, safety and strategic issue for the industry [4]. However, the life span and operating conditions of electrical cables are mainly relating to the life span of their insulation.
Indeed, the insulating tape is the direct element in contact with the external environment. Therefore, the insulating tape is the first defect element exposed to chemical, thermal (external) and mechanical deterioration [5]. The material used by L.C/Gecamines for the insulation of this external insulating tape is polyvinyl chloride (PVC).
Each electrical wire in a factory must be carefully covered with some type of electrical insulating tape (PVC in the case of this study). The wire itself is usually made of copper or aluminum, which are known to be good conductors of electrical power. The insulation must be opposite from the conductor; meaning, it must resist to electrical power and keep the latter in a path along with a conductor [6]. Insulated material can age, it can fail due to operating conditions, and it can cause inestimable damage to the plant.
The study gap is to evaluate the performance and life span of L.C/Gecamines cables subjected to a thermal force ageing to characterize their resistance to chemical attacks.
2. Materials and Methods
2.1. The Sample and LC/Gecamines Presentation
The L.C/Gecamines main office is a production entity of Gecamines Company in the Democratic Republic of Congo, engaged in the processing of non-ferrous metals (Figure 1 & Figure 2).
The insulated wire produced by L.C/Gecamines main office, was mainly composed of 99.73% copper and some other impurities at acceptable levels (Table 1). The wire-bars received by the headquarters from Shituru mining plant, had a deformation of ±2%. These wire bars were recycled in a FRITZ furnace at 400˚C - 450˚C for 3 hours of heating time, half an hour of holding and 18 hours of cooling. This operation resulted in new characteristic as shown in Table 2. The plastic materials in the form of pellets (PVC) had a density of 1.52 g/cm3; a low tensile strength of 13.6 MPa (15 MPa - 18 MPa for the supplier); an elongation at 200% breakage (280% for the supplier) and a continuous operating temperature of 70˚C to −5˚C for the L.C/Gecamines main office (Table 3). Noted that all these values (for plastic) from the supplier were define according to IEC 60,250 and SABS Methods 503/4/7.
![]()
Figure 1. L.C/Gecamines production diagram.
![]()
Figure 2. Sample of PVC insulated cables.
![]()
Table 1. Chemical composition according to the content of different metals in the conductor sample.
2.2. Studies Materials
BALTEAU apparatus were use in this study; it is a generator of medium voltage from zero to 10 kV, used for tests of dielectric rigidity of the insulator (Figure 3). The objective within was to determine the lifetime of cables based on the resistance of the insulation. A good insulation was defined as the insulation resistance that has a great value or equal to 1/100 of the applied voltage [7].
This lifetime is a function of the insulator’s resistance. The insulator must resist to the current, and maintain the latest in its trajectory along with the conductor.
2.3. Methods and Experimental Setup
In order to determine the resistance of the insulation, five samples (for each temperature) of 60 cm length and 9.075 mm2 cross-section were prepared and stripped at both ends; the central part of the sample was attach in the water bath (Figure 3(b)). The two ends were not in contact with the water (setup shown in Figure 4). The phase of the device was connect to the first stripped end of the
![]()
Table 2. Physical properties of annealed copper conductor.
![]()
Table 3. Characteristic of the PVC insulation of L.C/Gecamines cables.
![]()
Figure 3. BALTEAU insulation strength tester (a) and test bath (b).
![]()
Figure 4. Experimental setup for insulation strength testing.
cable and the neutral was immerse in the water bath. A voltage of 8 kV (8000 V) was sent through the cable (the time depends on the test to be performed).
During the study, the applied method was to determine the leakage current of the insulating tape than based on Ohm’s law, deduced the resistance of the insulating tape:
(1)
In order to evaluate the chemical attacks resistance, the used of a round bottom flask of 11, a principal solution, distilled water for dilution, a volumetric pipette, sulfuric acid, two beakers and a stopwatch. After the samples and the sulfuric acid solution’s preparation, these samples were immerse in an acid solution for 48 hours and then dried after 24 hours in an oven at 150˚C until a constant mass was obtain.
3. Results
3.1. Results Presentation on the Total Resistance of the Cable
The table shows 3940.88 Mega Ohms characterizes the resistance of PVC insulation. However, it should be noted that there is no such thing as perfect insulation (i.e., no insulation has infinite resistance); from that, a certain quantity of electricity always flows along or through the insulation to the outside environment. A good insulation essentially means a relatively high resistance to current. In order to describe an insulating material, a good insulation also means “the ability to maintain a high resistance” [8].
Having a look at the results obtained in Table 4, a confirmation come out that the isolation performed at L.C/Gecamines main office is good quality. Furthermore, if measured at regular time intervals, it is possible to monitor it degradation’s trends.
Table 5 shows the decrease in insulation resistance over time at 40˚C (near ambient temperature), 70˚C, 100˚C and 160˚C.
3.2. Estimated Lifetime of Insulating Tape in PVC
Table 4 below presented a highlighted lifetime of the insulation according to the different test temperature. Started from the graphical representation of each case, and then conducted through Excel, the trend line resulted to an equation of decrease’s evolution of the resistance according to time (Graphic 1).
Starting from the trend of the insulation resistance loss (plasticizer loss),
(with
: Determination graphical coefficient) where
Mega Ohms;
The lifetime would then be equal to:
Life hours corresponded to ± 50 years.
![]()
Table 4. Estimated total strength of the PVC insulation after the test.
![]()
Table 5. Insulation resistance of the cable at different temperatures according to a time interval.
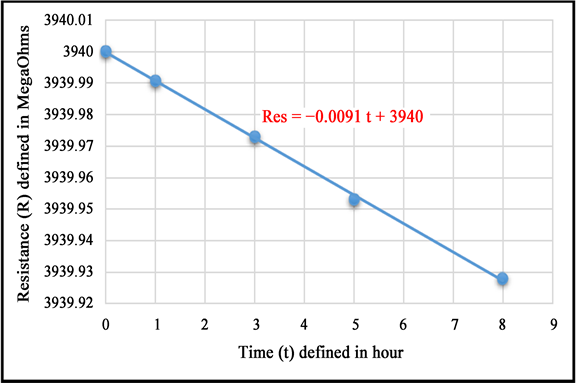
Graphic 1. Progress of PVC strength as a test time’s function at 40˚C.
According to this theory, the lifetime seems to be long because the main way of PVC insulation deterioration at this temperature consists in the evaporation of the plasticizer, the deshychloration is so low and even negligible. The Brebu’s work [9], who studied waste medium voltage cables (6 - 10 kV) after 18 years of operation, concludes that the PVC’s deshycloration is very low under service conditions. Indeed, according Hishler [8], it would take at least 2 billion years to have a release of 1% by mass of HCl at 40˚C. clearly, this estimate has no physical significance since the material itself will not survive that many years, but it does confirm that deshychloration of PVC is a negligible phenomenon at low, near ambient temperatures.
Graphic 2 shows the pattern of insulation resistance loss as a function of time, this pattern translates into the straight line
(with
: coefficient of graphical determination).
From this line, a lifetime of ±33 years is obtained. This loss of strength is largely due to the loss of plasticizer at 70˚C. However, in the case of PVC, the loss of plasticizer mass, as shown in the previous point, is mainly due to evaporation [5], Ekelund [10] studied the thermal ageing of a PVC electrical cable insulation. The results showed:
· The plasticizer (DEHP) loss process is controlled by evaporation below 100˚C;
· The evaporation rate of the plasticizer is constant in the studied time interval (150 days), looking at the strength loss curve, the trend of the line is almost linear, so its rate is constant also during 8 hours of research.
The trend of straight line of the decrease of the insulation resistance
(
: coefficient of graphical determination), inducted to a lifetime of 22 years (Graphic 3).
If the temperature is at 70˚C, the only mode of plasticizer loss was evaporation;
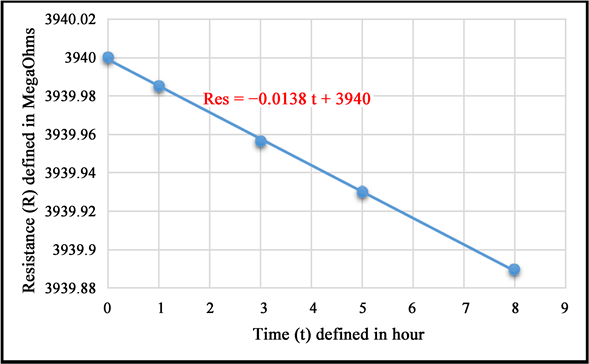
Graphic 2. Progress of the strength of PVC as a test time’s function at a temperature of 70˚C.
however, at 100˚C, this loss is largely due to evaporation of the plasticizer but also to a slight deshychloration. The Hishler’s work [8] shows a very low release off HCl below 105˚C (close to 100˚C) (Graphic 4).
The PVC insulation decrease resistance is show by the straight line
(with
: coefficient of graphical determination), this inducted a lifetime of ± 12 years.
This low lifetime obtained is justified by different aspects: at 160˚C, out from the loss of plasticizer (which is generally known), the PVC itself undergoes deterioration due to deshychloration as shown by the Ekelund’s work, between 120˚C and 180˚C, the deterioration of PVC in electrical cables consists mainly to a deshychloration. The latter is a bad phenomenon because it propagates by sequential removal of HCl molecules along the chain. Each removal creates a
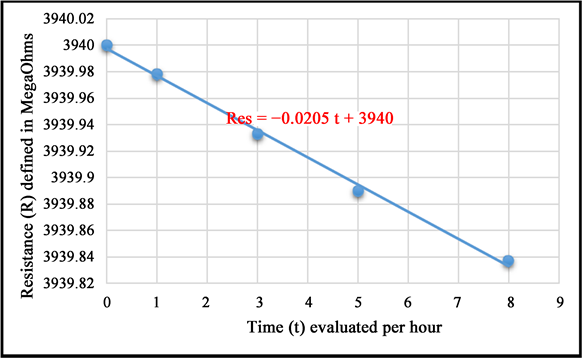
Graphic 3. Progress of the strength of PVC as a test time’s function at a temperature of 100˚C.
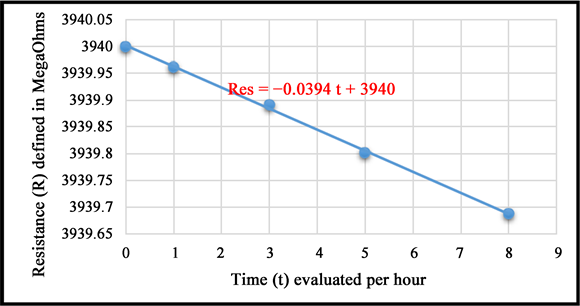
Graphic 4. Progress of PVC insulations resistance as a test time’s function at a temperature of 160˚C.
structural irregularity (double bond) that destabilizes the next monomer unit. Several deshychloration acts created polyene sequences along the chain that ultimately caused material’s yellowing and its thermal, optical and electrical properties changes [11].
3.3. Resistance to Acid Attacks
Each insulating tape’s presence constituents particularly affects the acid resistance value of the cables. Table 6 shows the change in mass of the samples after 48 hours test.
The above table shows that after 48 hours of immersion in sulfuric acid (pH 1.5 and density 1.84 g/cm3), a mass loss of 0.2470 g was observed, i.e. a rate of 2.027% per day. Thus, at a pH of 1.5; L.C cables have very poor resistance to acid attack. These results coincide with those proven by IPEX [12], performing a similar operation on PVC at 23˚C and 60˚C; the results showed that the PVC cable is non-resistant to 98% sulfuric acid attack but it states that it resists to sulfuric acid attack with a mass percentage of less than 80%. On the other hand, the commercial company Alfa Flex [13] proposes a good resistance of standard PVC from 10% to 50% mass of sulfuric acid, and a worst resistance for a higher massive percentage evaluated at 50% in acid. These operations were carried out at temperatures of 20˚C and 60˚C.
4. Conclusions
The present work is divided in two parts, the evaluation of the performance and the life span of LC/Gecamines cables subjected to a force thermal ageing and the characterization of their resistance to chemical attacks. The sample of the cable produced and insulated at LC/Gecamines has characteristics such as:
· The PVC: density is 1.52 g/cm3, a low tensile strength of 13.6 Mpa (between 15 Mpa - 18 Mpa indicated by supplier) and an elongation at break of 200% (200% - 280% indicated by supplier).
· Copper: a strain of 34.8%, a breaking load of 21.8 kg/mm2 (annealed material); a resistivity of 0.017 ohm mm2/m and a density of 8.93 g/cm3.
Therefore, the study of its performance and the accurate prediction of its lifetime remain economic, safety and strategic issues for the industries. Focusing on safety perspective, this work inscribed the objective to put LC cables in forced ageing in order to evaluate their performance and their life span in precarious conditions. This study used samples coming from cables produced and insulated in PVC at the main office of Gecamines Rolling Mills and Cable Factory. The results showed that the insulation carried out by the L.C/Gecamines main office is a great quality because the insulation resistances are high (i.e. 3940 Mega Ohms
![]()
Table 6. Results of the chemical attack test.
under normal conditions). The results showed a lifetime of more than 50 years at a temperature of 40˚C (close to an ambient temperature), ± 33 years at a temperature of 70˚C, 22 years at a temperature of 100˚C and ± 12 years at a temperature of 160˚C. For chemical attacks, the results showed that PVC cables have a poor resistance to sulfuric acid attack (having a pH of 1.5 and a density of 1.84 g/cm3). These results allow L.C/Gecamines’s customers to realize that is possible to order insulated electrical cables that can work in such extreme temperature conditions but also on short scale into higher acidic environment.